Industry professionals use metal finishing techniques to improve the functional and aesthetic qualities of metal parts and products. For stainless steel materials, electropolishing and passivation are two of the most popular finishing methods.
The two processes have some similarities, but ultimately, there are clear distinctions between them. Although both employ chemical baths in their operations, electropolishing also incorporates the use of an electrical current to remove microscopic surface layers of material to achieve a smooth finish, while passivation is non-electrolytic and produces a contaminant-free surface finish with enhanced corrosion resistance.
Depending on the part specifications, either process may serve as a finishing solution. However, deciding which one is most suitable for a stainless steel part requires a comprehensive understanding of how each process works and what material advantages it brings to the table. The following blog post provides an overview of the similarities and differences between electropolishing and passivation and considerations to keep in mind when choosing between the two for a stainless steel project.
Comparing Electropolishing and Passivation
As stated previously, electropolishing and passivation share a few process characteristics. The main similarity is that both processes are non-mechanical finishing methods that use chemical baths—rather than tooling—to achieve the intended surface finish. Beyond this quality, electropolishing and passivation diverge significantly.
The table below highlights some of the key differences between the two finishing processes.
Electropolishing
- Uses electrical current as part of the process
- Primarily used to remove a microscopic layer of surface imperfections and contaminants
- Can remove heat tint and/or oxide scales
Passivation
- Does not use electrical current in the process
- Primarily used to remove free iron and other surface contaminants
- Cannot remove heat tint and/or oxide scales
The passivation bath contains a diluted acid, typically nitric or citric acid, which dissolves surface contaminants. However, passivation differs from electropolishing in that there is no electric current involved in the process to strip the microscopic top layer from the metal’s surface.
With electropolishing, the metal is soaked in a temperature-controlled electrolyte bath while an electric current is applied. The combination of the chemical bath with the electrical current makes electropolishing more aggressive than passivation, allowing a uniform surface layer of the metal to be dissolved. The process strips away contaminants and smooths out burrs, sharp edges, and cracks to reveal a shiny, smooth, corrosion-resistant part. Unlike passivation, the electropolishing treatment also eliminates heat tint and/or oxide scales.
Choosing the Right Finishing Method
There are many factors to consider when choosing between passivation and electropolishing. Although industry professionals use both to remove surface contaminants, the two processes are very different and have their own benefits and limitations depending on the application. Selecting the appropriate finishing technique ultimately depends on the intended use of the stainless steel part.
When considering passivation for finishing, some important factors to keep in mind include:
- It removes manufacturing-related contaminants to restore the metal and enhance corrosion resistance.
- It cleans without brightening or altering the appearance of the metal.
- It is a gentler treatment than electropolishing and does not dissolve the outer layer of the metal.
- It enhances the protective oxide layer on the metal that prevents corrosion or rusting.
Some factors to consider when opting for electropolishing include:
- It is ideal when reverse plating or microscopic surface metal removal is needed.
- It allows for the complete removal of embedded contaminants by stripping the outer skin of the metal.
- It is excellent for finishing parts that have complex geometries.
- It is commonly used to finish metals that have applications in marine, medical, pharmaceutical, or food industries.
Exploring Electropolishing in More Detail
Although passivation certainly plays a vital role in metal processing, electropolishing often serves as a more intense and thorough treatment. One of the main drivers for choosing electropolishing over passivation is the superior surface finishes it provides. It deburrs, brightens, and allows for the selective removal of microscopic points (peaks), even in parts that are fragile or complex in design. Furthermore, it offers a higher degree of corrosion resistance than passivation by leaving the metal in a homogeneous and passive condition.
What makes electropolishing such an effective finishing method is the aggressiveness of the treatment. During the treatment process, the operator hooks the metal workpiece up to the positive terminal of the power supply to serve as the anode and the negatively charged cathode to the negative terminal. Once all components are assembled, they submerge the unit into a temperature-controlled electrolyte bath—typically containing a high-viscosity mixture of sulfuric and phosphoric acid—and apply an electric current. The combination of the chemical bath and electrical current results in the oxidation and dissolution of metal ions on the metal surface. This procedure allows for the removal of micron-level surface layers.
Some examples of metal parts that are commonly electropolished include:
- Blades and other cutting instruments
- Fasteners and pins
- Piping and tubing
- Springs
- Wire racks
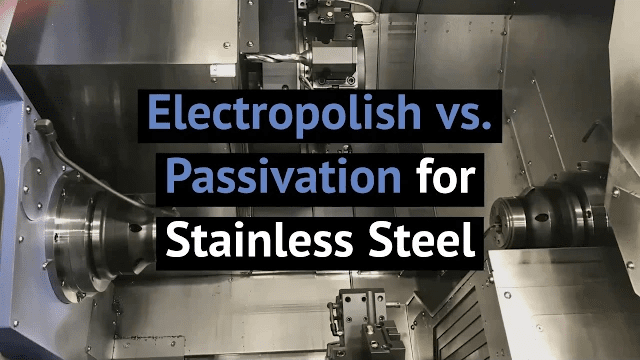
Stainless Steel Finishing Services at FZE Manufacturing
Electropolishing and passivation are non-mechanical, chemical finishing processes used to improve the functionality and/or appearance of metal parts. While both are valuable methods, they find use in different applications:
- Electropolishing is suitable when a more thorough process that allows for a superior level of smoothness, corrosion resistance, and durability is desired.
- Passivation is preferred when a less aggressive treatment is needed.
At FZE Manufacturing, we are a full-service machining and manufacturing company that assists customers with everything from product design and development to the delivery of completed parts. Our finishing capabilities include both electropolishing and passivation for stainless steel. To learn more about our finishing services and other capabilities, contact us or request a quote today.